What is Porosity in Welding: Best Practices for Preventing Permeable Welds
Unwinding the Enigma of Porosity in Welding: Tips for Reducing Issues and Making Best Use Of Quality
In the intricate world of welding, porosity stays a persistent difficulty that can substantially affect the high quality and integrity of welded joints. As we delve right into the depths of porosity in welding, revealing the secrets to its prevention and control will be critical for experts seeking to master the art of premium weldments.
Comprehending Porosity in Welding
Porosity in welding, an usual concern run into by welders, describes the presence of gas pockets or voids in the bonded material, which can compromise the honesty and high quality of the weld. These gas pockets are commonly entraped throughout the welding process because of various factors such as improper shielding gas, infected base materials, or inaccurate welding parameters. The formation of porosity can weaken the weld, making it at risk to cracking and deterioration, inevitably causing structural failings.
Recognizing the origin of porosity is crucial for welders to properly avoid its occurrence. By identifying the relevance of keeping correct gas shielding, guaranteeing the sanitation of base products, and enhancing welding settings, welders can dramatically decrease the chance of porosity formation. Additionally, making use of techniques like pre-heating the base product, using proper welding strategies, and conducting thorough assessments post-welding can further aid in reducing porosity issues. Generally, a comprehensive understanding of porosity in welding is necessary for welders to produce top notch and durable welds.
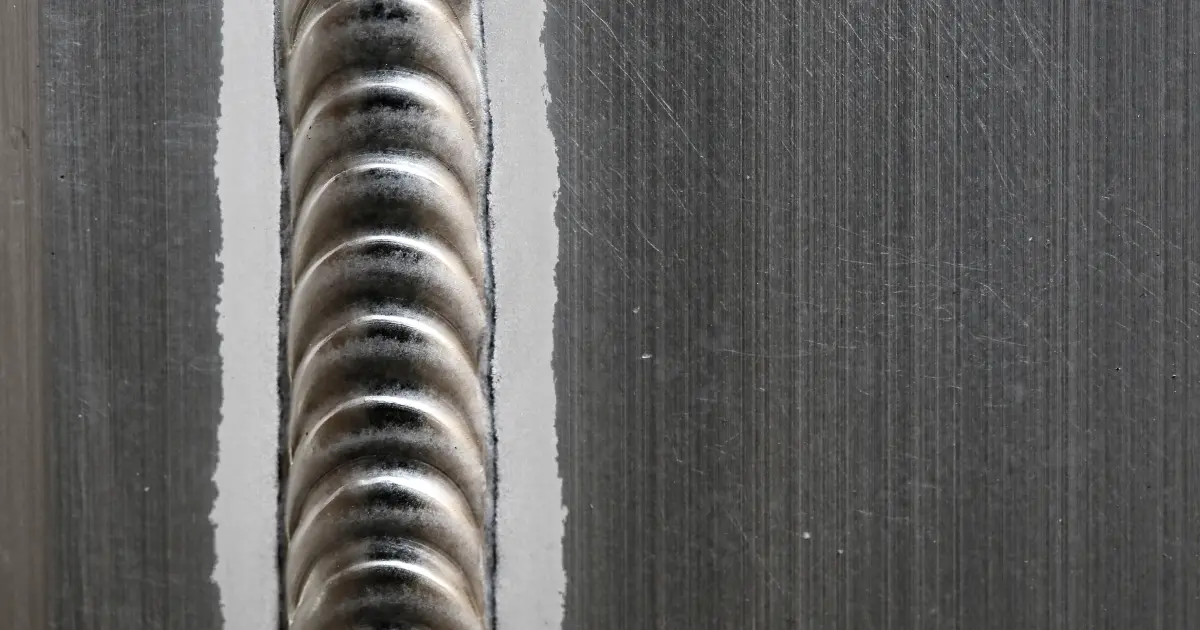
Typical Sources Of Porosity
When evaluating welding processes for prospective top quality concerns, recognizing the usual sources of porosity is necessary for maintaining weld stability and protecting against structural failures. Porosity, characterized by the presence of dental caries or voids in the weld steel, can dramatically compromise the mechanical buildings of a welded joint. One typical reason for porosity is inappropriate securing gas coverage. Inadequate shielding gas flow rates or incorrect gas combinations can lead to atmospheric contamination, leading to porosity formation.
Another widespread reason of porosity is the existence of dampness and contaminants on the surface area of the base steel or filler material. When welding materials are not effectively cleansed or are subjected to high levels of humidity, the evaporation of these pollutants during welding can create gaps within the weld bead. In addition, welding at incorrect specifications, such as exceedingly high travel speeds or currents, can produce extreme turbulence in the weld swimming pool, capturing gases and triggering porosity. By dealing with these common reasons via correct gas securing, material prep work, and adherence to ideal welding criteria, welders can lessen porosity and enhance the top quality of their welds.
Strategies for Porosity Avoidance
Implementing reliable safety nets is critical in lessening the occurrence of porosity in welding read the article procedures. One technique for porosity avoidance is guaranteeing appropriate cleansing of the base metal before welding. Impurities such as oil, grease, corrosion, and paint can lead to porosity, so detailed cleaning making use of suitable solvents or mechanical approaches is vital.

Using top notch filler products and securing gases that are suitable for the base metal and welding process can considerably minimize the threat of porosity. Additionally, preserving appropriate welding specifications, such as voltage, existing, take a trip rate, and gas circulation price, is essential for porosity prevention.
Furthermore, employing correct welding techniques, such as maintaining a consistent travel speed, electrode angle, and arc size, can help prevent porosity (What is Porosity). Ample training of welders to ensure they comply with ideal techniques and quality assurance treatments is additionally vital in reducing porosity problems in welding
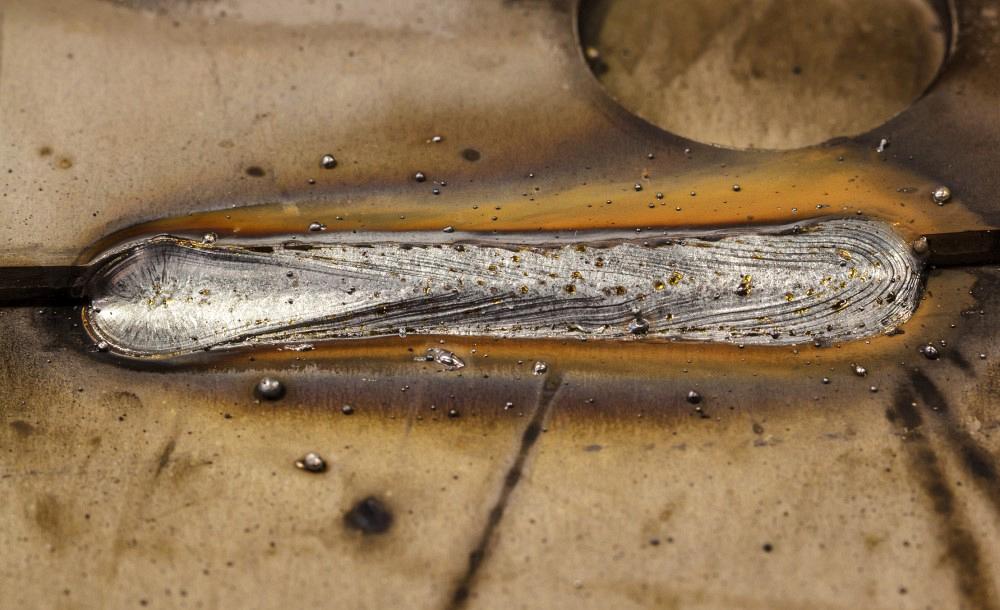
Ideal Practices for Quality Welds
One trick method is keeping browse around this site appropriate sanitation in the welding area. Extensively cleaning the workpiece and bordering area prior to welding can assist minimize these problems.
One more best technique is to meticulously choose the appropriate welding criteria for the certain materials being signed up with. This consists of establishing the appropriate voltage, current, take a trip rate, and protecting gas flow rate. Proper criterion selection makes certain ideal weld infiltration, blend, and total top quality. Using top notch welding consumables, such as electrodes and filler metals, can dramatically impact the final weld high quality. Buying costs consumables can result in more powerful, more sturdy welds with fewer issues. By complying with these ideal methods, welders can continually create high-quality welds that satisfy sector standards and surpass consumer expectations.
Relevance of Porosity Control
Porosity control plays an essential duty in ensuring the honesty and top quality of welding joints. Porosity, identified by the visibility of dental caries or spaces within the weld steel, can substantially compromise the mechanical residential properties and architectural stability of the weld. Extreme porosity deteriorates the weld, making it extra at risk to cracking, deterioration, and general failure under functional lots.
Efficient porosity control is necessary for maintaining the desired mechanical residential or commercial properties, such as strength, ductility, and sturdiness, of the bonded joint. What is Porosity. By lessening porosity, welders can improve the general top quality and reliability of the weld, ensuring that it satisfies the efficiency requirements of the desired application
Additionally, porosity control is essential for attaining the preferred visual appearance of the weld. Excessive porosity not just compromises More Bonuses the weld but additionally detracts from its aesthetic appeal, which can be important in industries where aesthetic appeals are very important. Proper porosity control techniques, such as utilizing the proper shielding gas, regulating the welding specifications, and ensuring appropriate cleanliness of the base products, are crucial for creating top quality welds with marginal problems.

Verdict
In verdict, porosity in welding is a typical flaw that can endanger the top quality of the weld. It is vital to control porosity in welding to guarantee the stability and stamina of the final item.